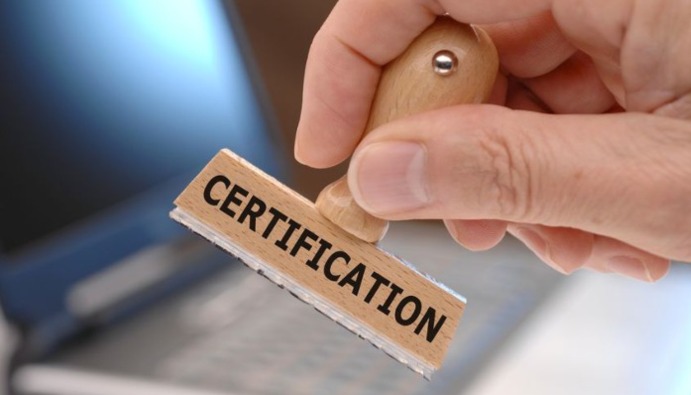
The Relationship Between Nonconformity Handling and Continuous Improvement
It is normal for organizations with a quality management system to encounter nonconformities and experience difficulties. Nonconformities experienced in organizations are an indication that some processes are not carried out according to plan and they need to be detected and corrected. Identifying nonconformities and finding solutions in organizations encourage continuous improvement activities.
Management of nonconformities is carried out together with continuous improvement and is one of the requirements of the quality management system. In order for the improvement to be sufficient, it is essential to identify the problems of the organization and seek solutions.
Non-conformity can be defined as any situation, product or service that does not comply with predefined standards. A defective product or inadequate service may be considered non-conformance in a business. According to the ISO 9001 standard, organizations must address nonconformities. The organization's goal should be to provide improvements and planning so that procedures do not fail again and are always carried out according to plan.
Although non-compliances are seen as a negative situation, they are an opportunity for the organization to improve. There should be a procedure for detecting nonconformities and a procedural follow-up system. The PDCA Cycle should be followed for continuous improvement and correct progress against nonconformities.
- Plan
- Do
- Check
- Act